SONOTRONIC GmbH
Becker-Goering-Str. 17-25
76307 Karlsbad, Germany
E-Mail: sales@sonotronic.de
Mon to Thu 8 am – 5 pm
Friday 8 am – 3 pm
Phone:
Ultrasonic thermofixing
Energy-saving textile finishing in the smallest of spaces
By using ultrasonic technology, ultrasonic thermofixing (UST) significantly reduces energy consumption and size as well as the amount of material used in the machine compared to conventional processes.
SONOTRONIC has projected the highly developed ultrasonic technology to a new application and developed an effective process for the thermal treatment of narrow fabrics. The innovation lies in the fact that the heat required for heat-setting is generated directly in the material by means of ultrasonic units.
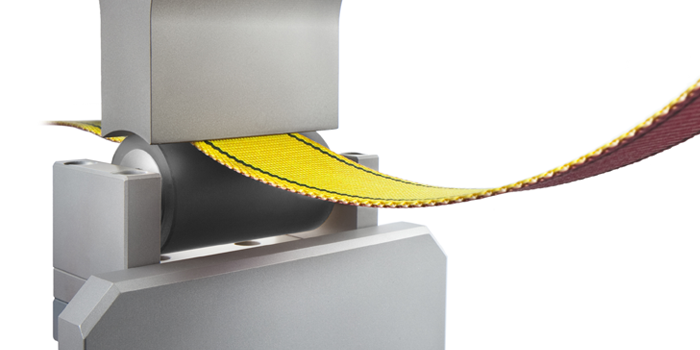
How does ultrasonic thermofixing work?
For this purpose, a generator converts the mains voltage into high-frequency high voltage and transmits it to the ultrasonic converter. The converter electrostrictively converts the incoming voltage into mechanical vibrations of the same frequency and transmits them via the transformer (booster) and sonotrode (welding tool) into the material. Absorption of the vibrations causes interfacial and molecular friction in the joining zone when pressure is applied and the mechanical vibrations are introduced vertically. The result is a local heating of the material made of, for example, PA, PES, PP as well as mixed fabrics.
In the patented ultrasonic thermofixing process, the material is continuously drawn between an anvil, which generates a controlled contact pressure, and the sonotrode. The heat generated by the ultrasonic vibrations brings the material directly to the required temperature from within. The ultrasonic also causes a calendering effect in the material. Coordinated drives upstream and downstream of the ultrasonic units transport the material and generate any necessary tensile stress in the strip. This maintains a specified shrinkage or stretching of the material.
Schematic structure of an ultrasonic thermofixing machine
No preheating with ultrasonic technology
The ultrasonic thermofixing is particularly characterized by its flexibility: Due to the direct mode of operation of the ultrasonic, the system is very quickly at the maximum temperature and speed, which allows the machine to be stopped and started at any time. Long preheating and the associated effective energy loss are eliminated. Overall, the energy input for ultrasonic thermofixing is reduced by up to 90 percent compared to conventional processes, as the ultrasonic has a very intensive effect on the material: The necessary heat is generated in a fraction of a second.
As a result, only a few meters of material are in the machine during the heat-setting process, which ultimately results in a correspondingly compact design. Furthermore, the use of ultrasonic thermofixing machines makes it possible to treat even smaller quantities of material. The parameters can be stored in the control system in relation to the product and called up at any time.
Example: Untreated strip (left) and ultrasonically thermofixed strip (right)
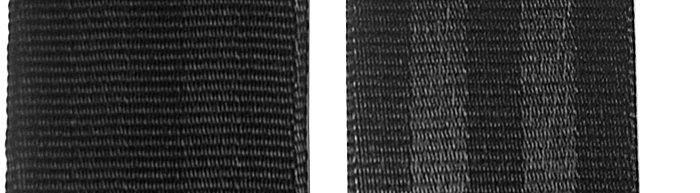
Advantages
- Energy savings of up to 90 %
- Compact design
- Thermofixing and calendering by ultrasonic
- Precise control of material width
- Novel product possibilities
- Flexible response to market requirements
- Efficient treatment of smaller material quantities
- Fast start and stop of the machine with almost no material loss
- Maximum throughput speed of up to over 100 m/min
Applications
- Thermofixing, stretching and shrinking of:
- Tapes, yarns, twines, ropes and cords
- PA, PES, PP, cotton, aramid, Dyneema®
- Blended fabrics