SONOTRONIC GmbH
Becker-Goering-Str. 17-25
76307 Karlsbad, Germany
E-Mail: sales@sonotronic.de
Mon to Thu 8 am – 5 pm
Friday 8 am – 3 pm
Phone:
Ultrasonic
Environmentally friendly and energy-efficient joining technology
Ultrasonic technology, compared to other thermal processes, is fast, efficient and environmentally friendly in the processing of thermoplastics, films and fabrics. Our products are used in all plastic processing industries, for example automotive interior and exterior, filtration, hygiene, technical textiles, packaging, but also in environmental technology.
How does ultrasonic work?
The ultrasonic frequency is generated in a generator. The generator converts mains voltage into high-frequency high voltage and transmits this to the oscillating unit, which consists of the converter, the booster (amplitude transformation piece) and the sonotrode (welding tool). The converter electrostatically converts the incoming voltage into mechanical oscillations of the same frequency and transmits them to the workpiece via the booster and sonotrode. Absorption of the vibrations causes interfacial and molecular friction in the joining or separating zone when pressure is applied and the mechanical vibrations are introduced vertically. The result is local heating of the workpiece material in the joining zone. This plasticization allows one or more workpieces to be welded either continuously or in cycles, punched, riveted or embossed.
In addition, ultrasonic offers another application in environmental technology with the treatment of biosolids: instead of local heating, ultrasonic creates intense cavitation bubbles in the liquids. The implosion of the cavitation bubbles affects the liquid and thus better converts or sterilizes e.g. biological mass.
The ultrasonic generator produces the electrical ultrasonic oscillations: To do this, it raises the mains voltage from 230 volts to approximately 1,200 volts. In addition, the generator increases the frequency of the AC voltage from 50 hertz to 20,000 to 35,000 hertz. It transfers this to the oscillating unit, which consists of a converter, a booster (amplitude transformation piece) and a sonotrode.
The converter transforms the incoming electrical oscillations into mechanical oscillations of the same frequency. Via the booster, which keeps the mechanical oscillation the same or amplifies it, it reaches the sonotrode. The sonotrode is the actual welding tool; it moves 20,000 to 35,000 times per second by a few micrometers and introduces the ultrasonic vibrations into the part.
When the mechanical vibrations are introduced vertically and pressure is applied, the plastic absorbs the vibrations in the joining zone. This friction in the interface and the molecules causes local heating in the joining zone of the material, so that one or more workpieces can be ultrasonically welded, riveted, cut or punched.
Technologies
Ultrasonic weldingRegistration for training
We offer training for the qualified use of our technologies and machines at the company location in Karlsbad, via webinar or at your site.
What is the frequency of ultrasonic?
Ultrasonic is a mechanical vibration with a frequency of 16 kHz to 1 GHz. Sonic below 20 kHz is perceptible to humans and is therefore referred to as auditory sound. Frequencies above 500 kHz are hypersonic. For industrial use in plastics processing, ultrasonic can be used in the low frequency range of 20 kHz to 100 kHz. SONOTRONIC's ultrasonic systems operate at 20 kHz, 30 kHz or 35 kHz.
Which plastics can be processed with ultrasonic?
Plastics consist of polymerized hydrocarbons. The macromolecules of the plastics are more or less entangled next to each other and are not crosslinked (thermoplastics), weakly crosslinked (elastomers) or strongly crosslinked (thermosets). (Source: www.kunststoffe.de)
Thermoplastics (plastomers) are the only plastics that are weldable
Thermoplastics are plastics that can be formed within a certain temperature range. This is done by heating them up to the molten state. In addition, the deformation can be repeated as often as desired (reversibly) by cooling and reheating. Thermoplastics are mainly used for injection molded parts and extruded parts. Thermosets and elastomers cannot be welded with ultrasonic.
Thermoplastics are divided into amorphous and semi-crystalline plastics
Plastics whose molecules are not arranged in regular crystal lattices are referred to as amorphous (Greek = without shape). Partially crystalline plastics have both ordered crystalline and amorphous regions in their morphological structure (source: Plastics basics).
Amorphous plastics
Amorphous plastics are usually hard and have a favorable transmission coefficient for ultrasonic vibrations (oscillations). For this reason, it is possible to bring the introduced energy to the seam over greater distances. Less energy is required for processing amorphous plastics compared to semi-crystalline plastics.
Filament molecules of amorphous thermoplastics
Examples amorphous thermoplastics
ABS (Acrylonitrile butadiene styrene )
- Car door
- Instrument panel
- Spoiler
- Hubcaps
PMMA (Poly(methyl methacrylate))
- Reflectors on bicycle wheels
- Airplane discs
- Bite splints in dental technology
- Traffic signs
PC (Polycarbonate)
- Eyeglass lenses
- CDs
- Visors (ski goggles or helmets)
ASA (Acrylonitrile styrene acrylate)
- Exterior trim parts (car)
- Garage doors
- Air conditioner housing
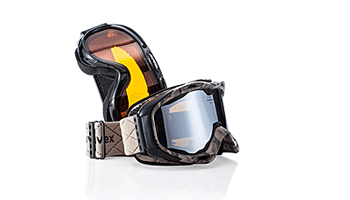
Semi-crystalline plastics
Semi-crystalline plastics are polymers whose molecules tend to arrange themselves into "building blocks" of a crystal structure in the transition phase between liquid and solid state. They have an unfavorable transmission coefficient for ultrasonic vibrations, therefore no or only conditional far-field welding is possible.
Filament molecules of semi-crystalline thermoplastics
Examples semi-crystalline thermoplastics
PA (Polyamide)
- Lamp housing
- Fuel line in car
- Expansion tank in car
- Accelerator/brake pedal in car
POM (Polyoxymethylene)
- Tanks
- Handles in furniture
- Kitchen fittings
- Loudspeaker grilles
PP (Polypropylene)
- Bicycle helmets
- Films/packaging in the food industry
- Bumper
PE (Polyethylene)
- Films/packaging in the food industry
- Simple injection molded parts like canisters or tubes
- Orthopedic corsages
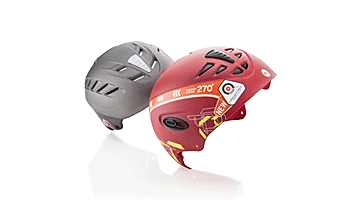