SONOTRONIC GmbH
Becker-Goering-Str. 17-25
76307 Karlsbad, Germany
E-Mail: sales@sonotronic.de
Mon to Thu 8 am – 5 pm
Friday 8 am – 3 pm
Phone:
Infrared machines
Contactless, particle-free and high-strength joining technology
With infrared welding, SONOTRONIC offers a process that complements ultrasonic very well. If required by the material properties of the parts, the standard and special machines are equipped with infrared units.
To satisfy the market requirements, SONOTRONIC has optimized the characteristics of infrared technology. Given a heating time of approx. 6 – 12 seconds, the power required is only 80 watts. Even the joining forces have been reduced and can be adjusted by an external pressure regulator. The mechanical components have been designed to be compact and interchangeable to achieve stable processes.
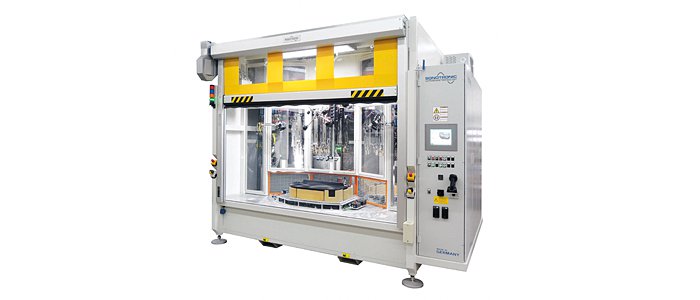
To further improve the results, the design of the joining geometries and their surroundings must also be considered in infrared riveting. This requires close cooperation between the machine manufacturer and the customer. SONOTRONIC provides competent advice on the component-specific requirements for infrared riveted joints.
In addition, complete solutions can be realized in combination with ultrasonic and infrared feed units (hybrid machines). A classic example of this is loudspeaker grilles made of POM, which are inserted into door panels in addition to other parts. The innovative infrared riveting process has already been used several times in customer-specific systems on the market. Hybrid machines with ultrasonic and infrared, as well as special machines with more than 50 infrared feed units have been realized.
This machine concept offers various standardized designs, e.g. with crank drive, NC axis, bridge with crank drive and C-frame (insertion area accessible from all sides)
Advantages
- Infrared units by an experienced special machine manufacturer
- Compact design compared with existing market solutions
- Infrared lamp highly efficient by focusing the infrared rays
- Clearly reduced joining forces with process control using embossing depth
- Heating and embossing in one position (without moving)
- View of riveting position when setting up
- Heating position of infrared lamp can be adjusted by hard stop; position maintained, even after changing the lamp (no adjustment necessary)
- Quick change of the infrared lamp possible
- Integrated purge air and electrical control
- No smoke
Applications
- Door panel
- Instrument panel
- Center console
Processes
- Infrared riveting
- Contactless heating of materials
- Welding of different materials
Flexible machine concepts
iSONIC FLEXFor you to download
Flyer
Flyer Infrared riveting
You might also be interested in
Contact
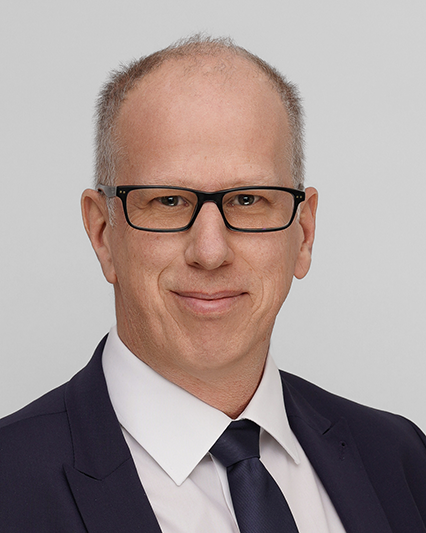