Four different sectors of the German middle class with one mission: to guarantee the current supply of protective masks. SONOTRONIC Nagel GmbH has equipped a complete production line with ultrasonic systems for this purpose. In further cooperation with theFraunhofer IPT from Aachen and the mechanical engineering company IBF Automation from Freudenberg, Moss GmbH commissioned the production line. The aim: to produce up to 600,000 high-quality masks per day, assembled with ultrasonic, and all of them 100% Made in Germany.
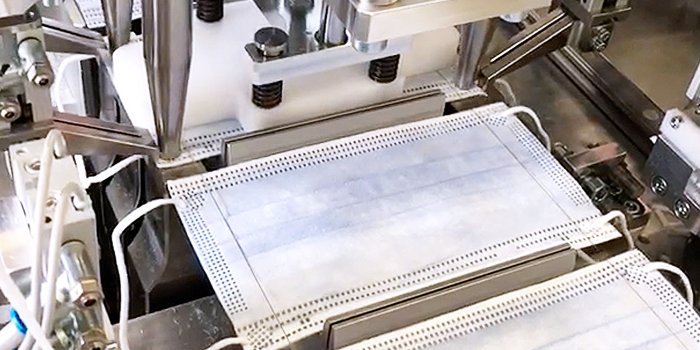
The commitment of SONOTRONIC in this project focused on the efficient integration of the ultrasonic tools that weld the nonwovens together. In addition to the joining of the materials, high process reliability and short cycle times were important here. Thus five ultrasonic oscillating units weld the three-layer masks and a rotating embossing roller generates the seam contour. The wrinkling and fastening of the elastic ear bands is also carried out automatically, using systems developed by the Fraunhofer Institute. The protective masks, certified according to European standards, are currently being produced on the prototype line. In the coming weeks, eleven more machines will be manufactured for the European and American markets. Correspondingly, production will be expanded according to this manufacturing principle.
The ultrasonic components are manufactured one hundred percent at SONOTRONIC's company site in Karlsbad, Germany, according to high quality standards, thus ensuring high availability and short delivery times. The use of ultrasonic for the classic production of face masks as well as for the manufacture of FFP masks and hygiene and protective equipment is an environmentally friendly solution in addition to the economic aspect. This is because production is energy efficient and does not require the use of other materials such as adhesives.
At the end of this mission, the good partnership was highlighted by Moss CEO Bottenberg. "Thanks to the competent and very helpful nature of the SONOTRONIC service staff, we were able to understand and also adapt many processes much more quickly. From the quotation phase to shipping and above all to support, we have rarely experienced such a reliable and fast partner. Without your help and the entire team, we would not be where we are," he added with praise. And the other participants also agreed: "Great cooperation" in times of change.
As an example of this successful cooperation, the ultrasonic manufacturer SONOTRONIC has equipped over the past few weeks further companies with ultrasonic tools and is thus making an active contribution against the spread of Covid-19. In this context, the Federal Office for Civil Protection and Disaster Assistance already awarded the title "Operator of Critical Infrastructures (KRITIS)" in April.
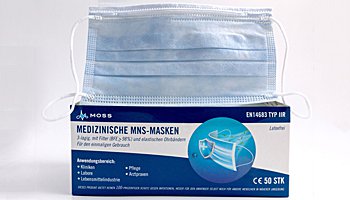
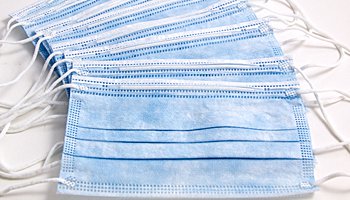
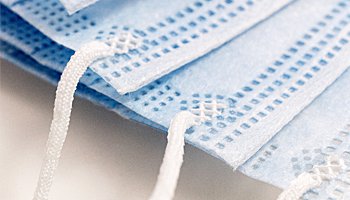
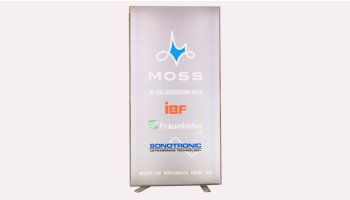