For 20 years, PFAFF Industriesysteme und Maschinen GmbH from Kaiserslautern has relied on the ultrasonic welding components from SONOTRONIC Nagel GmbH, Karlsbad, and is now using them in the new fully automatic, CE-compliant mask system. The result: a solid and mature production line (made in Germany) that guarantees process reliability. And this at an output of up to 4,000 mouth and nose protection masks per hour.
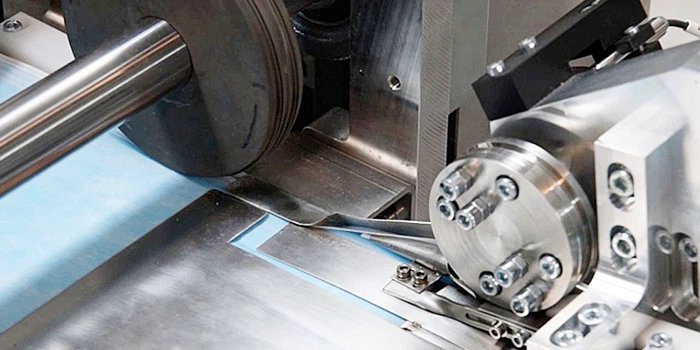
In response to the increasing demand for protective masks in the current corona pandemic, engineers and technicians have reacted and jointly developed a machine concept that meets the requirements of "German engineering" in a unique way. The product not only incorporates 150 years of expertise in joining textile materials, but also the concentrated know-how of the PFAFF INDUSTRIAL, KSL and SONOTRONIC brands in the fields of process control, automation and robotics. The configuration is carried out via a Siemens control system with 3 HMIs / operator panels. The mask system is equipped with ultrasonic components from SONOTRONIC for continuous and intermittent welding. These ensure fast and reliable processing of nonwovens, nosebands and earbands for the production of masks. All drives are synchronized and controlled by servo motors. A special feature of this type of machine is the optimized process control, which, in addition to safe operation, also achieves a very low noise level. Therefore, no further noise protection is necessary.
The technical data at a glance:
- Mask size: 175 x 95 mm
- Production output: up to 70 masks per minute
- 1-, 2- or 3-layer processing (filter/nonwovens)
- Siemens control with 3 HMIs
- Ultrasonic welding components from SONOTRONIC
- All drives with synchronized servo control
- Optimized process control achieves very low noise emission – no further noise protection required
PFAFF is considered a pioneer in the field of ultrasonic roll seam welding of textiles. The traditional company from Kaiserslautern still uses ultrasonic welding components from SONOTRONIC, a specialist for ultrasonic plastic joining since 1974. In times of Covid-19, it is important to use the right equipment for mask production to avoid cost-intensive readjustments.
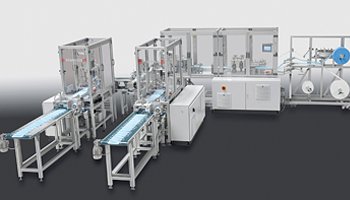
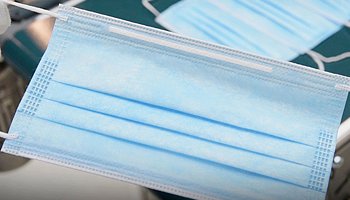
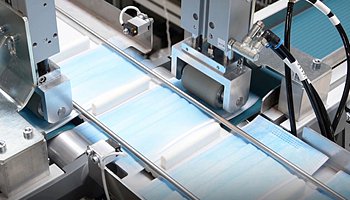
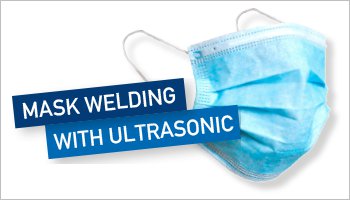