SONOTRONIC GmbH
Becker-Goering-Str. 17-25
76307 Karlsbad, Germany
E-Mail: sales@sonotronic.de
Mon to Thu 8 am – 5 pm
Friday 8 am – 3 pm
Phone:
Toys
100 % fun thanks to safe welding processes with ultrasonic
Product safety is an absolute priority in this industry. Other requirements for toys are functionality, protection against injuries, but of course also the beautiful appearance. Ultrasonic welding passes the absolute endurance test in this respect. This is also the case, for example, with the toys from Bruder GmbH. With the aim of ensuring that the Personal Water Craft does not sink, Bruder Spielwaren GmbH & Co. KG has found a reliable partner in the field of plastic joining in SONOTRONIC.
The requirement: Tight welding of ABS plastic injection molded parts
The result: Tight ultrasonic welding without markings
In this application, the hull and cover of a watercraft are welded together absolutely watertight using ultrasonic. On the components, a tongue-and-groove joint with energy director forms the weld seam and ensures a tight weld. This preserves the hollow space and guarantees that the water toy will not sink.
Realized applications are for example
- Water toys made of plastics such as boats, kayaks, etc. welded tightly with ultrasonic
- Ultrasonic welding of toy figures in compliance with safety requirements
- Ultrasonic series production of toy comic characters
- Ultrasonic welding of promotional items such as reflector bears tightly and densely
- Automated production of plastic toys: injection molding machine - robot handling - ultrasonic welding machine iSONIC ECO with acoustic protection hood
Industry solutions
Automotive engineeringYou might also be interested in
Contact
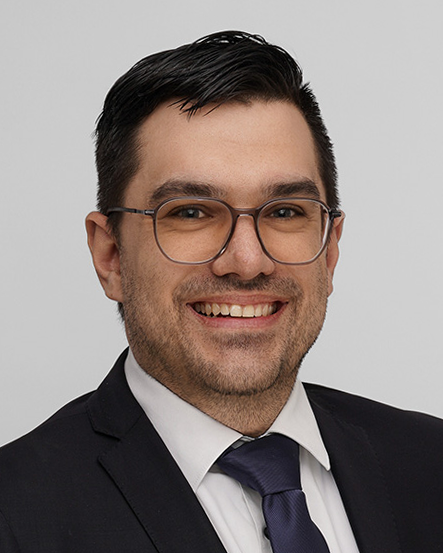